The 7 Wastes of Lean
Lean practitioners commonly agree on the 7 wastes of lean. Improvement projects that focus on these 7 elements saves company's resources. Which in turn saves your company time and money.
We classify these waste as
- Transportation
- Inventory
- Motion
- Waiting
- Over-Production
- Over-Processing
- Defects.
To remember these use the name...Tim Wood.
For kicks, start a Tim Wood improvement project at your company and see your fellow employees raise their eyebrows. Everybody will want to know who is this Tim Wood. Tell them that you want to eliminate Tim Wood from the company because he never shows up but he causes all kinds of problems.
Lets expand on the 7 wastes
Transportation. The act of moving product between different operations. For a service organization this could be moving customers, employees and data between different areas. Why is transportation a waste?
Transportation. The act of moving product between different operations. For a service organization this could be moving customers, employees and data between different areas. Why is transportation a waste?
- You do not add value to the product as it is being moved
- Movement time costs the company money.
- Possible product damage during the movement.
- Possible product misplacement.
- Unnecessarily waste of energy to move the product.
- Costs of moving product including carts, bins, rollers and automation.
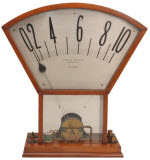
Inventory. Building more than you sell. Also, buying more than you need. Why is excessive inventory a waste?
- Inventory takes unnecessary space.
- Money spent on inventory can be used in more worthwhile endeavors.
- When problems occur with the product, product inventory is suspect and needs to be reviewed.
- Inventory delays identification of problems. Many times issues with WIP is found much later than the manufacturing step that caused the problem.
- Increases lead times because product A inventory WIP slows down the delivery of product B.
- It cost money to store inventory including bins, carts, shelves, etc.
Motion. Excessive movement by employees and machines. This occurs during the actual value added step of the process.
- Motion causes extensive processing time due to walking, lifting, and reaching.
- Motion can cuase injuries from exessive lifting, stretching, and bending.
- Motion delays communication.
Waiting. The dead time between value added steps. Waiting significantly adds to overall processing time of the product or service.
- Similar to inventory, WIP that waits take unnecessary space.
- Money invested in the product sits idle during waiting.
- Waiting slows down delivering the product to the customer and getting paid for the product.
- Waiting time can never be recovered.
- Waiting causes inventory to build.
Over-Production. This one of 7 waste occurs when you manufacture or provide service before its needed. Many companies over produce because they do not want their equipment to sit idle.
- Over-Production, similar to inventory, makes the company spend money on unnecessary product.
- It prevents a balance production flow.
- It causes scheduling errors.
- Also see Inventory Wastes.
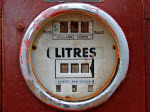
Over-Processing. This is act of providing unnecessary excess value to the customer or using expensive over-kill equipment to manufacture the item.
- Company invested unnecessary money into the equipment acquisition.
- Company invested unnecessary money into the added product feature.
- Maintenance and repairs is more expensive and more downtime than simpler equipment.
- Unnecessary training and employee qualification for the added features and equipment.
- More difficult to implement balance production flow because equipment can't be moved or the added features complicate the production flow.
- The more complicated the item, the more chances for mistakes and defects.
Defects. A product or service that doesn't meet the requirements.
- Rework of the product causes excessive cost, time and delays
- Scrap of the product causes excessive cost, time and delays
- Cost associated with MRB, Segregating, and re-isnspection.
- Customer dissatisfaction from rescheduling, corrective action, and the supplier's lost of production capacity.
- Decrease employee morale due to rework and rebuilding.
A Tim Wood improvement project takes one or more elements from these 7 wastes and focuses on improving the situation or eliminating the issue. By understanding the 7 waste of lean, one knows where to put the effort for improvement projects.
Below we list some improvement ideas to address the 7 wastes.
Below we list some improvement ideas to address the 7 wastes.
Transportation
- Layout floor so the next station is directly next to the previous value added station.
- Assure location of the item goes to a clearly labeled, color coded, pre-define location.
- Use value added flow diagrams to track product, employee and data movement.
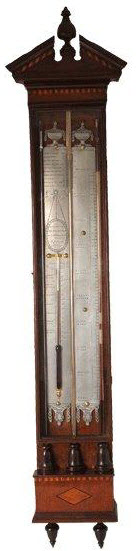
Inventory and Over-Production
- Purchase only material for current orders.
- Build only to current orders.
- Stop equipment and employees immediately when customer needs are met.
- Minimize work quantities. Lot size of 1 unit is best.
- Stop production immediately as soon you discover a problem.
- Train employees on multiple processes and equipment.
Motion
- Implement Human Ergonomics to minimize excessive human movement
- Implement 5S to make known location of all items.
Waiting
- Minimize work quantities. Lot size of 1 unit is best.
- Implement JIT manufacturing and use a pull system for manufacturing.
- Shut down equipment when down stream inventories are building.
- Move employees from low production areas to areas where material waits for processing.
Over Processing
- Find simpler solutions to manufacturing
- Don't over design the product.
- Include customer feedback during product design to eliminate unnecessary features.
- Include employees who conduct the processing in the equipment purchasing decisions.
Defects
- Use the continuous improvement tools
- Apply the 8D approach to solving problems
- Use pareto charts for attributes
- Use control charts for variable
- Implement a system of process and product auditing
- Design quality into the product
- Constantly train and retrain
Read more: http://www.quality-assurance-solutions.com/7-wastes.html#ixzz2A18EMnAQ
Tidak ada komentar:
Posting Komentar